National Science and Technology Development Agency | National Nanotechology Center
Research
Chemical production
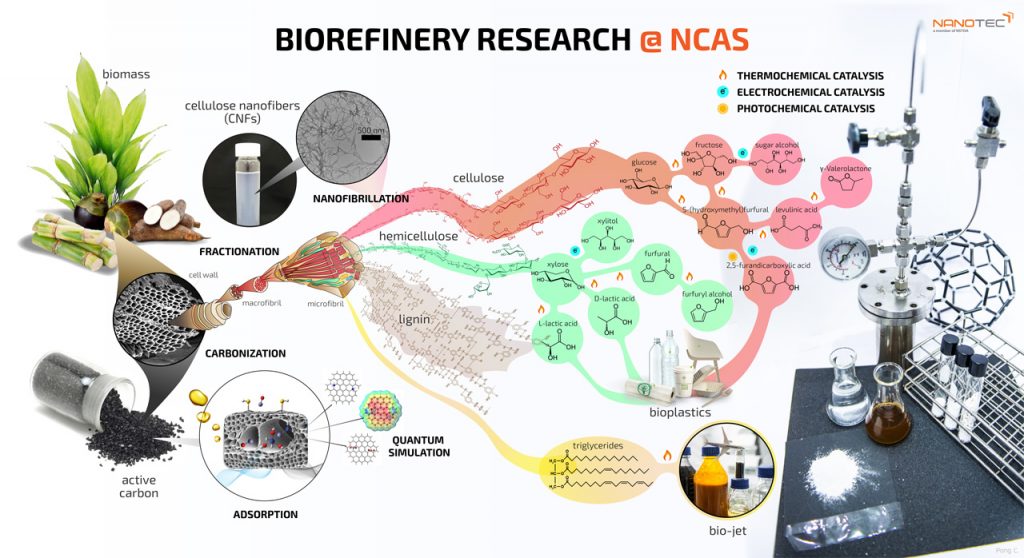
A sustainable economy requires renewable resources and “Lignocellulosic Biomass” as plant-based raw materials are the only renewable carbon-rich source available on the Earth. To divert the chemical production from fossil fuels to these renewable feedstocks, new processes must be developed since these plant-derived precursors have high oxygen contents requiring lower temperature chemistry. We have established R&D of biochemicals production through thermochemical, electrochemical, and photoelectrochemical processes utilizing nanocatalysis and DFT simulation for designing & engineering catalysts and chemical reactions. Some of our key research includes the production of lactic acid, 5-hydroxymethylfurfural (5-HMF), and 2, 5-furandicarboxylic acid (FDCA).
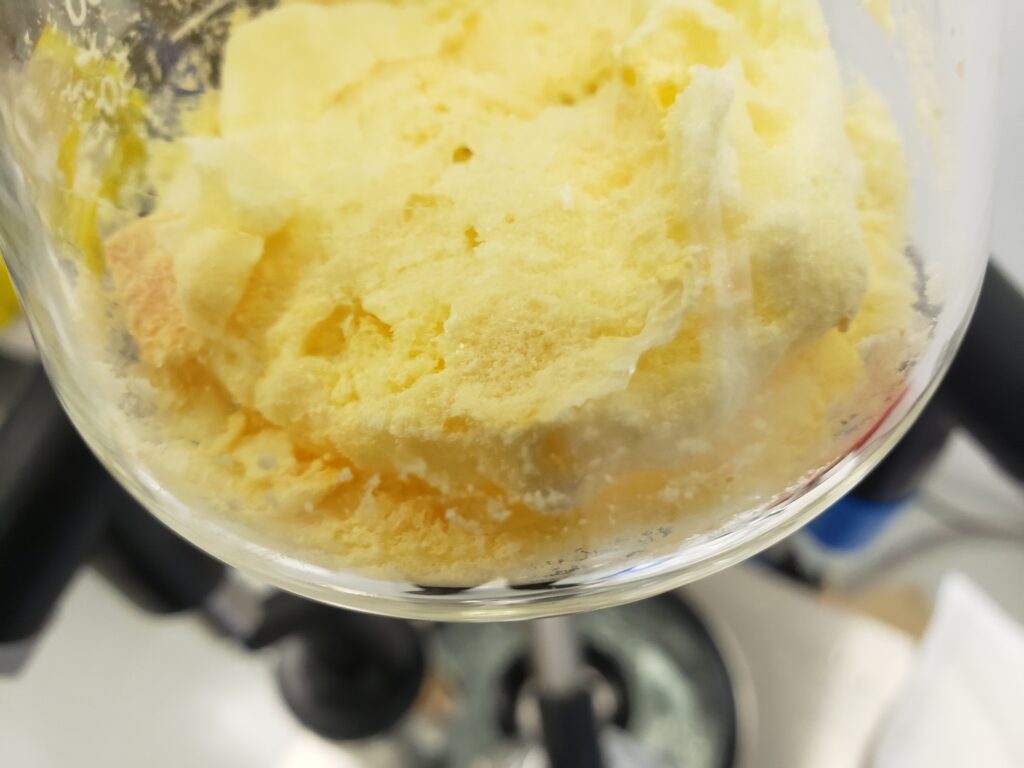
5-HYDROXYMETHYLFURFURAL
HMF or 5-hydroxymethylfurfural is the key platform chemical that can be converted to a wide variety of important products. In terms of production, HMF can be produced from a wide range of sugars. We conducted extensive research on HMF production based on thermochemical catalysis of sugars employing both homogeneous and heterogeneous catalysts to obtain HMF in high yield and purity. Mainly, we focus on the catalyst and process design as well as process optimization at different production scales. We also focus on the separation and purification of the HMF product using techniques such as solvent extraction, vacuum distillation, crystallization, chromatography, adsorption and membrane.
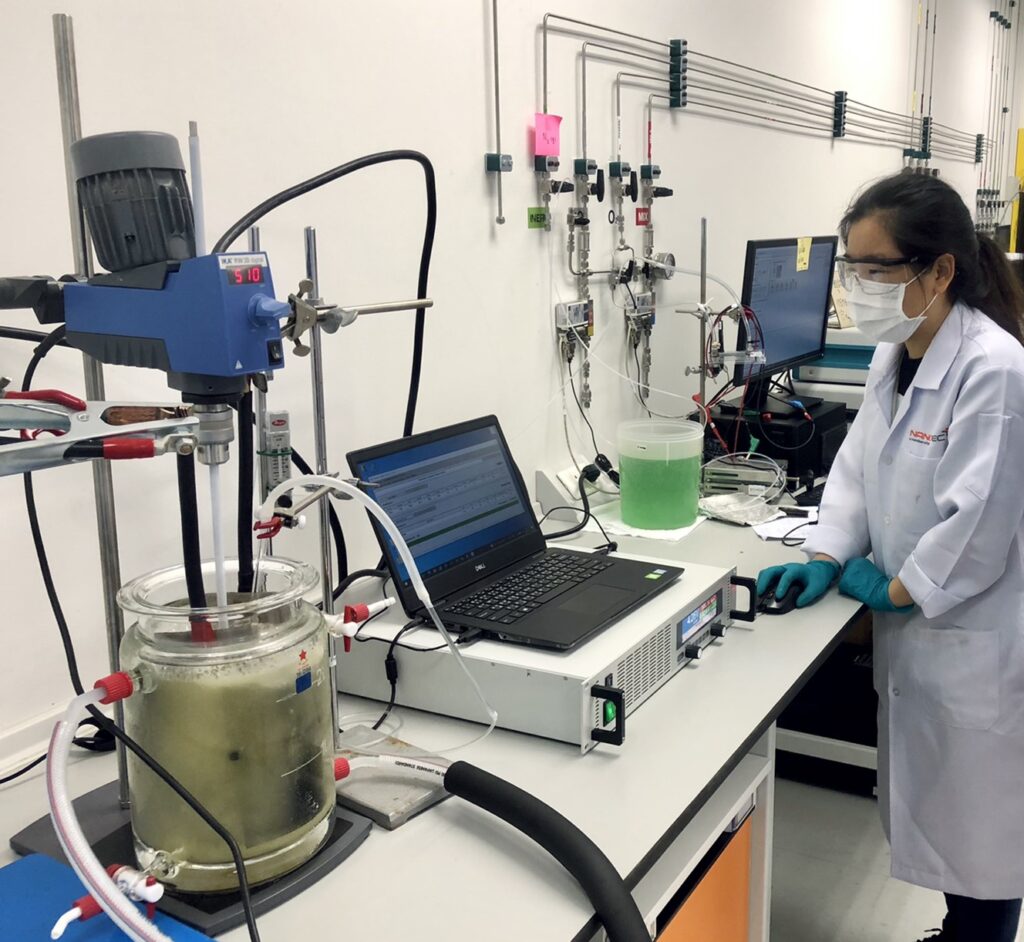
2,5-FURANDICARBOXYLIC ACID
FDCA or 2,5-Furandicarboxylic acid has emerged as an important platform chemical that can be used as a monomer for plant-based polymers such as polyethylene furanoate (PEF) (a substitute for polyethylene terephthalate), a pharmaceutical intermediate, and a corrosion inhibitor. However, the synthesis of high purity FDCA with an economical and sustainable process is a challenge. We have embarked on two different approaches including thermochemical and electrochemical production of FDCA. The research encompasses catalyst design and process design to achieve high purity of FDCA in large-scale production.
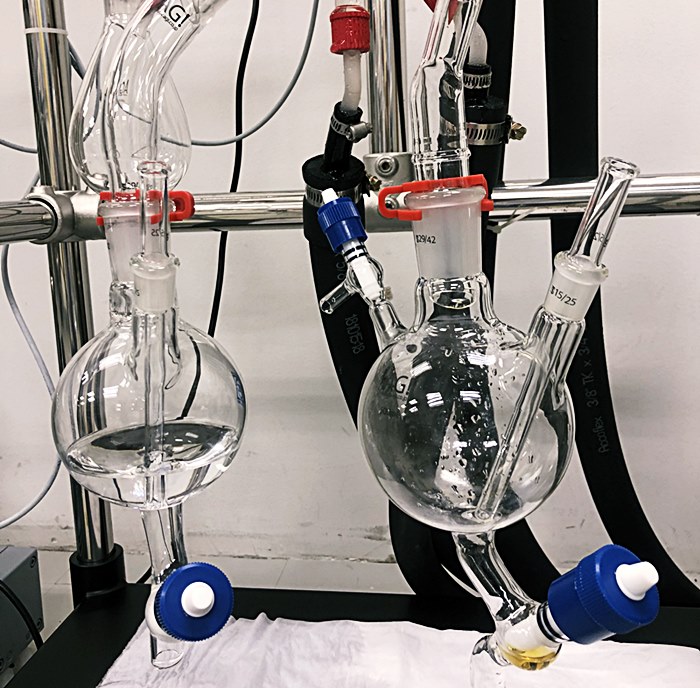
LACTIC ACID
Lactic acid has long been considered as one of the most important building-block intermediates which is widely used in food, pharmaceutical, cosmetic and (biodegradable and biocompatible) polymer industries. We employ catalyst design and separation technology for efficient production of lactic acid both in batch and continuous reactors with sub-kg/day capacity.
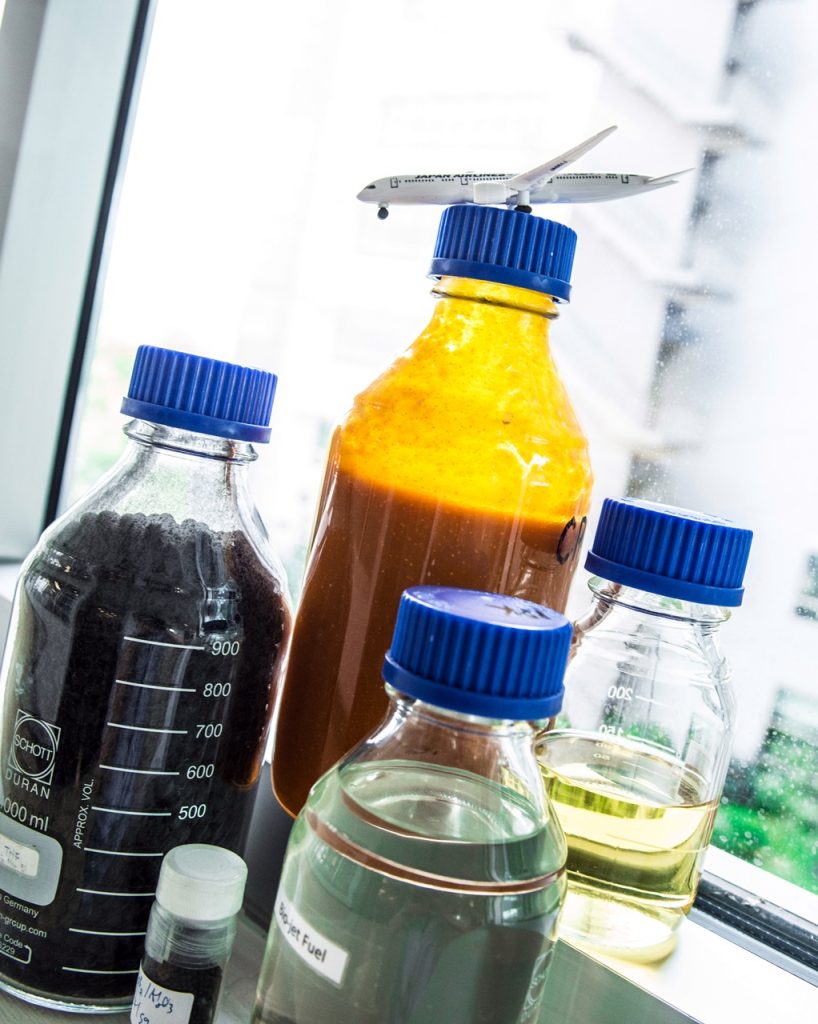
BIOFUELS
Triglyceride-based feedstocks (e.g. fat, oil, fatty acid) and lignocellulosic biomass derivatives have been considered promising renewable resources for the production of advanced biofuels such as green diesel and biojet fuels as well as oleochemicals. We have expertise in the catalyst and process design for the production of bio-hydrogenated diesel (BHD) and biojet fuel using supported and unsupported deoxygenation catalysts with isomerization-cracking property. We also obtained insights into the underlying performance using density functional theory (DFT) calculation. Our patented solution for large-scale processing of supported metal sulfide catalysts has been licensed and is currently in use on a pilot plant at the customer’s site.
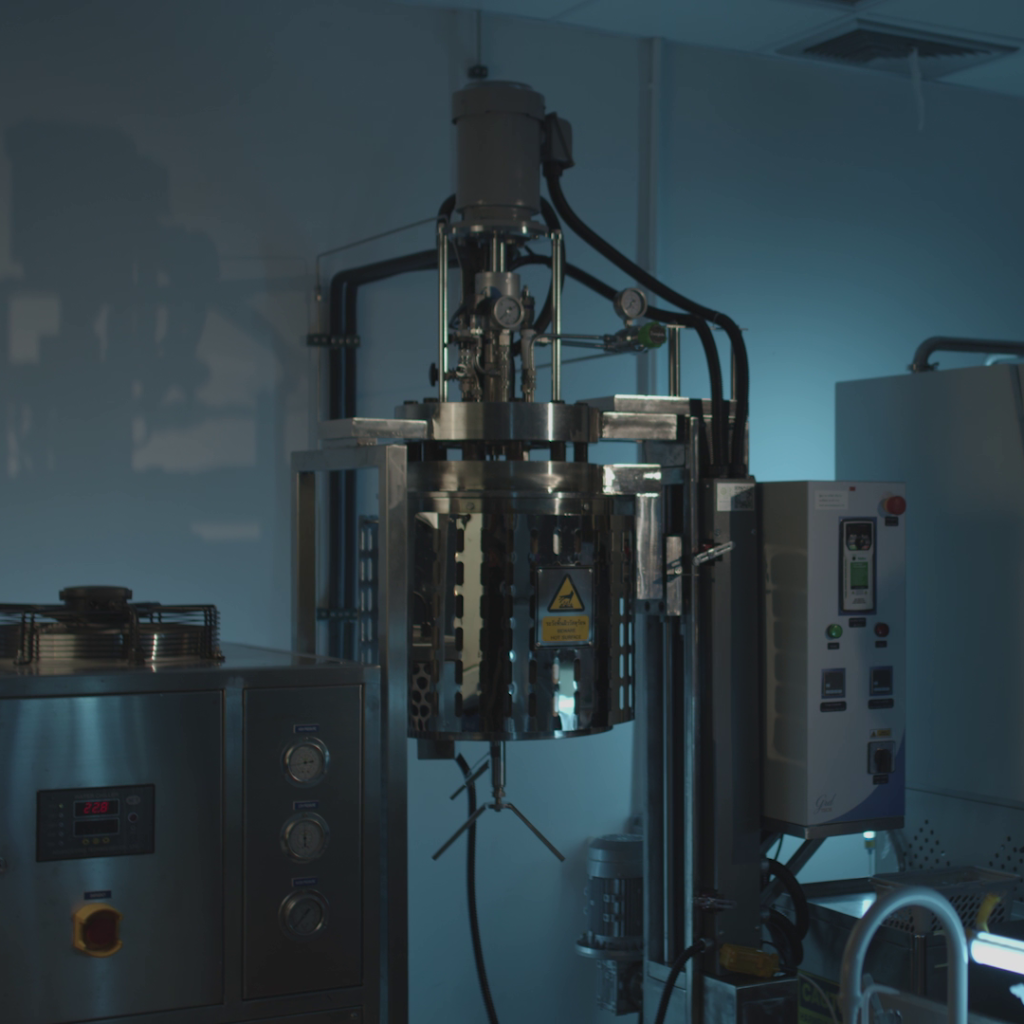
PRE-PILOT AND PILOT-SCALE PRODUCTION
The main goal of our research group is to transfer the technology from laboratory to industry. However, the gap with high risk and high cost exists between these stages also known as the Valley of Death. We have developed several high-pressure reactors ranging from 50 mL to 13 L that can withstand temperature upto 350 oC and compressed gas up to 100 bar to aid the transition. The production rate can be varied from 100 grams to 1 kilogram per batch depending on the conditions. We also have continuous flow reactors that can uptake both liquid and gas feeds. The reactors can operate at the maximum temperature of 500 oC and pressure of 40 bar compressed gas. Online and offline chromatographic analyzers are available on site. Besides, we take part in the design of EECi-Biopolis at Rayong, Thailand for pilot-scale production up to 250 L.